Project Info
COMPLETE
Project Title
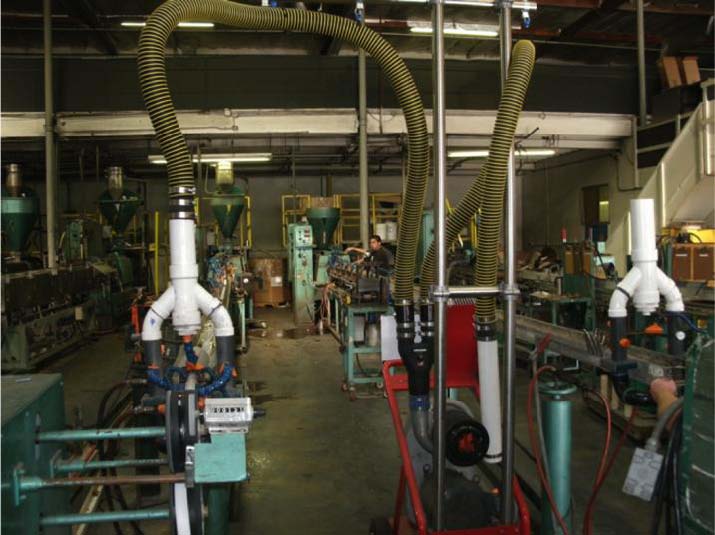
Blower for Industrial Applications
Project Number ET10SCE1160 Organization SCE End-use Process Loads Sector Industrial Project Year(s) 2010 - 2011Description
Compressed air systems are common in most industrial facilities in California. They use considerably more energy and are very inefficient when they are applied to some industrial processes that blowers can perform. The scope of this project is to replace/modify existing compressed-air to blowers for selected industrial processes, such as drying or cleaning products. Blowers typically uses ¼ to 1/10 of energy compared to compressed-air on those applications.
Project Results
Compressed air systems, used to increase the pressure of air by reducing its volume, are useful and valuable among various commercial, agricultural, and industrial markets. However, they can be an expensive and often an inefficient solution when applied inappropriately and when not maintained for optimal performance. In an effort to promote the appropriate application and optimal performance of these systems across all markets, the Compressed Air Challenge (CAC), a voluntary collaborative entity, was first organized in 1997 to encourage best practices for compressed air system uses. Despite CAC’s efforts for over a decade, many industrial customers are still struggling with the appropriate and optimal uses of compressed air systems, which can be very costly. Unfortunately, because of their versatility, compressed air systems are very often used for open-blowing type production processes such as cooling, drying, removing debris, and cleaning. These common uses can be done more effectively and economically by using actual air blowers, which in many cases provide significant energy and potential 1 demand reductions, using only about one-quarter to one-tenth the energy of compressed air systems. Therefore, it is the focus of this project to evaluate the potential for energy and demand reduction associated with the conversion of compressed air systems to blower air systems, for open blowing in industrial usage.
A field assessment was conducted at a thermoplastic manufacturing plant, called the Amesbury Bandlock Products, located in the city of Ontario, California. This site was selected because it uses compressed air exclusively for open blowing applications like cooling and removing water cooling) from its products. Like many open blowing applications, its production process does not require a high pressure amount of air. Test conducted on December 8 and December 31, 2010 demonstrated that 80% to 90% of energy savings can be achieved by converting inappropriate use of compressed air to blower air for open blowing processes. Table 1 summarizes the field assessment results.
Project Report Document
Loading PDF Preview...