Project Info
COMPLETE
Project Title
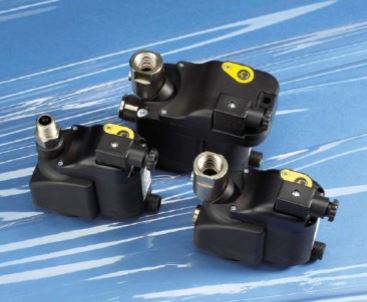
Zero Loss Compressed Air Drains
Project Number ET13SCE1140 Organization SCE End-use Process Loads Sector Industrial Project Year(s) 2013 - 2015Description
No-loss drains expel condensate from compressed air systems, with no associated loss of compressed air. They typically are installed at the compressor, air dryer, filter, storage tank, or at any low point in the piping where moisture might collect. No-loss drains open a valve only when signaled by the condensate level control. The more common timed drains, an alternative to no-loss drains, periodically on a pre-set timed basis, open a drain valve releasing compressed air along with condensate, which wastes compressor energy. The planned tested measure installs ZLD on a compressor system, replacing the existing timer drains. Zero loss condensate drains allow for the release of condensate without the loss of compressed air which saves air compressor energy.
Project Results
Compressed air is often considered industry's "fourth utility" after electricity, gas, and water, and is both a necessity and a major cost in manufacturing and light industrial facilities. It is used extensively as a source of power for tools, equipment, and industrial processes in the chemicals, plastics, glass, pulp and paper, electricity generation, textiles, petroleum, automobiles, and aircraft industries. Importantly, the users of compressed air in the small business segments, which is the focus of this report, that have compressors primarily in the 150 HP or less range are in need of a simple, fast, and cost-effective way to optimize their compressed air energy usage. These customers represent a large and underserved market opportunity for reduced energy usage. A survey prepared for the Energy Trust of Oregon states that “Compressors 100 HP and smaller represent 75-85% of the industrial market.”
The goal of this project was to evaluate the energy savings potential of Zero Loss Drains (ZLD) in typical small air compressor applications predominantly (150 HP or less) within Southern California Edison (SCE) service territory. Although the entire range of compressor sizes and types can benefit from Zero Loss Drains, this assessment focused on a very specific and large market segment – smaller compressors. The small users are also characterized as a hard-to-reach market and represent significant untapped savings.
Maintaining system pressure is a constant load on air compressor(s) of all sizes. The need for periodic scheduled condensate purging of the lines based on timer-drains is a continuous source of system air loss, and essentially a system-wide and planned leak. This systemic air loss can be eliminated with the use of zero-loss drain (ZLD) traps.
The energy savings are achieved by retrofitting existing timer-operated standard condensate drains with “zero-loss” condensate drains on air compressor systems. The purpose of the analysis was to evaluate deemed savings value(s) for the replacement of timer drains with zero energy loss drains. Currently, SCE recognizes the saving potential from ZLDs and provides its customers incentives through the customized solution process (Solution Code, PR87504) at a rate of $0.08/kWh and $100/kW. However, one key market issue that a deemed savings approach can address, is that customers are not participating in a customized approach due to the added time, complexity and cost of that process. Regardless of the large savings potential, it is not being realized. Therefore, in order to realize an increased market share for ZLDs, avoid lost opportunity and transform the market from the standard Timer Drains, it is essential to establish reasonable deemed savings values.
Any energy savings claims must be based on measured and documented results. The measured savings achieved as a result of this evaluation can ultimately be used as a basis to provide prescriptive utility incentives that encourage other customers to implement this technology. The purpose of the analysis is to establish the deemed savings values for the replacement of timer drains with zero energy loss drains.
A representative sample of twelve (12) SCE customer locations with an average two (2) ZLDs installed per site from a mix of local industries shown in Figure 1, were utilized to demonstrate this technology. The project was conducted in steps to capture: 1) “as-is” or pre-installation of ZLD performance based on timer drain settings, 2) post-installation of ZLD performance, and 3) energy efficiency (EE) measure analysis of data to demonstrate savings.
Baseline performance and drain settings were determined utilizing an intake questionnaire and site audit for existing timer drains settings. Installation issues were identified, and the incumbent timer drains were removed. Following the intake assessment, new zero loss drains were installed and the baseline was determined to document the performance of the equipment, as it would normally operate with zero loss drains installed. The measure case is installing a zero-loss condensate drain on a compressor system, replacing the existing timer drains. The energy savings where analyzed on a “per drain” basis. There is only one baseline period.
Project Report Document
Loading PDF Preview...